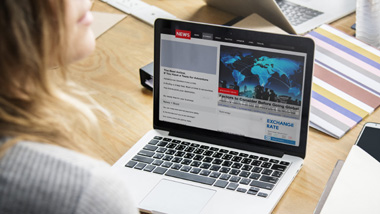
NEWS
The combustion of polymers is a highly intense and complex thermal oxidation reaction, characterized by the emission of thick smoke or intense flames. The general process of combustion is that under the continuous heating of an external heat source, the polymer first undergoes a chain reaction of free radical degradation with oxygen in the air, producing volatile combustibles. When the substance reaches a certain concentration and temperature, it will ignite and burn. Part of the heat released by the combustion is supplied to the polymer being degraded, further intensifying its degradation and producing more combustible gases. The flame will quickly spread and cause a large fire in a short period of time.
Flame retardants are a type of additive that can prevent plastic from igniting or suppress flame propagation. According to their usage methods, flame retardants can be divided into two categories: additive and reactive. Additive flame retardants are added to plastics during the processing and are commonly used in thermoplastic materials. Reactive flame retardants are monomers chemically bonded to polymer molecular chains during polymer synthesis, and are commonly used in thermosetting plastics. Some reactive flame retardants can also be used as additive flame retardants. According to their chemical structure, flame retardants can be divided into two categories: inorganic and organic. These compounds often contain halogens and phosphorus, and some contain elements such as antimony, boron, and aluminum.
1. The flame retardant effect of flame retardants refers to the ability to prevent or inhibit the rate of physical or chemical changes in polymer materials during combustion. Specifically, these effects are reflected in the following aspects.
(1) The endothermic effect makes it difficult for the temperature of polymer materials to rise. For example, borax has 10 molecules of crystal water, and the release of crystal water takes up 141.8 kJ/mol of heat. Due to its endothermic effect, the temperature rise of the material is suppressed, resulting in a flame retardant effect. The flame retardant effect of hydrated alumina is also due to its endothermic effect caused by thermal dehydration. In addition, some molten droplets generated during the cracking of thermoplastic polymers can also have a certain flame retardant effect by removing the heat of reaction from the combustion zone.
(2) The covering effect is to generate a stable covering layer at a higher temperature, or decompose to form a foam like material, which covers the surface of the polymer material, making it difficult for the heat generated by combustion to pass into the material, making it difficult for the combustible gas generated by the thermal decomposition of the polymer material to escape, and isolating the material from the air, so as to inhibit the cracking of the material and achieve the flame retardant effect. Phosphate ester compounds and fire-resistant foam coatings can function according to this mechanism.
(3) Dilution effect: Such substances can produce a large amount of non combustible gases when thermally decomposed, causing the combustible gases produced by polymer materials and oxygen in the air to be diluted and unable to reach the flammable concentration range, thereby preventing the ignition and combustion of polymer materials. CO2, NH3, HCl, and H2O can be used as diluting gases. Phosphate amine, chloride amine, carbonate amine and other non combustible gases can be produced when heated.
(4) The transfer effect changes the mode of thermal decomposition of polymer materials, thereby suppressing the production of flammable gases. For example, using acid or alkali to dehydrate cellulose and decompose it into charcoal and water, as it does not produce flammable gases, it cannot ignite and burn. Amine chloride, amine phosphate, phosphate ester and other substances can be decomposed to produce these substances, which catalyze the carbonization of materials and achieve flame retardant purposes.
(5) Inhibition effect (capturing free radicals), the combustion of polymers is mainly a chain reaction of free radicals. Some substances can capture active intermediates such as HO ·, H ·, · O ·, HOO · in the combustion reaction, inhibit the chain reaction of free radicals, and reduce the combustion rate until the flame is extinguished. Common organic halogen compounds such as bromine and chlorine have this inhibitory effect.
(6) Enhancement effect (synergistic effect): Some materials, if used alone, have no flame retardant effect or have little flame retardant effect. Multiple materials can be used in combination to enhance flame retardancy. The combination of antimony trioxide and halogen compounds is the most typical example. As a result, not only can the flame retardant efficiency be improved, but the amount of flame retardant used can also be reduced.
2. The flame retardancy of materials is often achieved through mechanisms such as gas-phase flame retardancy, condensed phase flame retardancy, and interrupted heat exchange flame retardancy. Gas phase flame retardant that inhibits free radicals that promote the growth of combustion reaction chains and exerts flame retardant function; It belongs to condensed phase flame retardant that delays or prevents the thermal decomposition of high polymers in the solid phase and plays a flame retardant role; The flame retardant caused by taking away some of the heat generated by polymer combustion belongs to the category of interrupted heat exchanger flame retardant. However, combustion and flame retardancy are both very complex processes that involve many influencing and constraining factors. It is difficult to strictly classify the flame retardant mechanism of a flame retardant system into one. In fact, many flame retardant systems work simultaneously with several flame retardant mechanisms.
2.1 Gas phase flame retardant mechanism Gas phase flame retardant system refers to the flame retardant effect that interrupts or delays the chain reaction of combustion in the gas phase. The following situations of flame retardant belong to gas phase flame retardant.
(1) Flame retardant materials can generate free radical inhibitors when heated or burned, thereby interrupting the chain reaction of combustion.
(2) Flame retardant materials generate fine particles when heated or burned, which can promote the binding of free radicals to terminate chain combustion reactions.
(3) Flame retardant materials release a large amount of inert gas or high-density vapor when heated or burned. The former can dilute oxygen and gaseous combustibles, and lower the temperature of this combustible gas, causing combustion to stop; The latter covers the combustible gas, isolating it from contact with air, thus suffocating combustion. Volatile, low boiling point phosphorus containing compounds, such as trialkylphosphine oxide (R3PO), belong to gas-phase flame retardants. Mass spectrometry analysis shows that triphenylphosphonic acid ester and triphenylphosphine oxide decompose into free radical fragments in the flame, which capture H · and O · free radicals like halides, thereby inhibiting the combustion chain reaction. In the combustion and cracking of red phosphorus, P · is also formed, which reacts with oxygen in the polymer to form phosphate ester structures. In addition, the expansion flame retardant system may also play a role in the gas phase, where amine compounds can decompose into NH3, H2O, and NO when heated. The first two gases can dilute the oxygen concentration in the flame zone, while the latter can quench the free radicals necessary for combustion, leading to the termination of chain reactions.
2.2 Condensed phase flame retardant mechanism refers to the flame retardant effect produced by delaying or interrupting the thermal decomposition of flame retardant materials in the condensed phase. The following situations of flame retardant belong to condensed phase flame retardant.
(1) Flame retardants delay or prevent the thermal decomposition of combustible gases and free radicals in the condensed phase.
(2) Inorganic fillers with high specific heat capacity in flame retardant materials prevent the material from reaching the thermal decomposition temperature through heat storage and conduction.
(3) Flame retardants decompose and absorb heat, slowing down or stopping the temperature rise of flame retardant materials.
(4) When flame retardant materials burn, a porous carbon layer is formed on their surface, which is flame retardant, heat-insulating, and oxygen isolating. This layer can also prevent combustible gases from entering the combustion gas phase, requiring sufficient oxygen and combustible gas mixture to maintain continued combustion during combustion. If the free radicals generated by thermal cracking are intercepted and disappear, combustion will slow down or be interrupted. When flame retardant thermoplastic containing organic bromide as a flame retardant burns, the following reactions occur. RH → R ·+H · chain triggers HO ·+CO=CO2+H · chain growth (highly exothermic reaction) H ·+O2=HO ·+O · chain branching O ·+HBr=HO · -+Br · chain transfer HO ·+HBr=H2O+Br · chain termination. Highly reactive HO · radicals play a critical role in the combustion process. When HO · is replaced by Br · with poor reactivity, the free radical chain reaction terminates.
2.3 Interruption of Heat Exchange Flame Retardant Mechanism This refers to taking away some of the heat generated by the combustion of flame-retardant materials, causing the materials to be unable to maintain their thermal decomposition temperature and thus unable to produce combustible gases, resulting in self extinguishing combustion. For example, when flame retardant materials are subjected to strong heat or combustion, they can melt, and the molten material is prone to dripping, thus taking away most of the heat and reducing the heat feedback to the body, resulting in delayed combustion and possible termination of combustion. So, the combustibility of easily melted materials is usually low, but the dripping hot liquid droplets can ignite other substances, increasing the risk of fire.
3. Flame retardant mechanisms of several typical flame retardants
3.1 Halogen based flame retardants include bromine based and chlorine based flame retardants. Halogen flame retardants are currently one of the largest organic flame retardants produced in the world. Most of the halogenated flame retardants are brominated flame retardants. Bromine based flame retardants used in industrial production can be divided into three categories: additive, reactive, and polymer, with a wide variety of varieties. There are currently over 20 types of additive brominated flame retardants, over 10 types of polymer brominated flame retardants, and over 20 types of reactive brominated flame retardants available in both domestic and international markets. The main types of additive flame retardants are decabromodiphenyl ether (DBDPO) Tetrabromobisphenol A bis (2,3-dialkylpropyl) ether (TBAB), octabromodiphenyl ether (OBDPO), etc; Reactive flame retardants mainly include tetrabromobisphenol A (TBBPA), 2,4,6-tribromophenol, etc; Polymer flame retardants mainly include brominated polystyrene, brominated epoxy, tetrabromobisphenol A carbonate oligomers, etc. The main reason why bromine based flame retardants are favored is their high flame retardant efficiency and moderate price. Due to the low bond energy of C-Br bonds, the decomposition temperature of most bromine based flame retardants is between 200 ℃ and 300 ℃, which is exactly the decomposition temperature range of commonly used polymers. So during the decomposition of polymers, bromine based flame retardants also begin to decompose and can capture the free radicals generated during the decomposition of polymer materials, thereby delaying or inhibiting the reaction of the combustion chain. At the same time, the released HBr itself is a refractory gas that can cover the surface of the material, playing a role in blocking and diluting oxygen concentration. This type of flame retardant is invariably used in combination with antimony based compounds (antimony trioxide or antimony pentoxide), and the synergistic effect significantly improves the flame retardant effect. Halogen flame retardants mainly exert flame retardant effects in the gas phase. Because the hydrogen halide gas produced by the decomposition of halides is non combustible and has a dilution effect. It has a high specific gravity, forming a layer of air film that covers the solid surface of polymer materials, which can isolate air and heat and have a covering effect. More importantly, hydrogen halides can suppress the chain reaction of polymer material combustion and play a role in clearing free radicals. Taking bromide as an example, its mechanism for inhibiting free radical chain reactions is as follows: brominated flame retardants → Br · Br ·+RH → R ·+HBr HO ·+HBr=H2O+Br · The brominated flame retardants added to polymer materials undergo decomposition reactions when exposed to fire and heat, generating free radicals Br ·, which in turn react with the polymer material to produce hydrogen bromide. Hydrogen bromide reacts with highly active OH · radicals, regenerating Br and reducing the concentration of OH · radicals, suppressing the chain reaction of combustion and slowing down the combustion rate until it is extinguished. However, when a fire occurs, the decomposition and combustion of these materials produce a large amount of smoke and toxic corrosive gases, causing a "secondary disaster". The combustion products (halides) have a long atmospheric lifespan and are difficult to remove once they enter the atmosphere, seriously polluting the atmospheric environment and damaging the ozone layer. In addition, the combustion and cracking products of polymer materials flame retardant with polybrominated diphenyl ethers contain toxic polybrominated dibenzodioxanes (PBDD) and polybrominated dibenzofurans (PBDF). In September 1994, the US Environmental Protection Agency evaluated and confirmed that these substances were toxic to humans and animals.
3.2 Flame retardant mechanism of phosphorus and phosphorus compounds Phosphorus and phosphorus compounds have been used as flame retardants for a long time, and their flame retardant mechanism has been studied earlier. Initially, it was found that materials using phosphorus containing flame retardants would generate a lot of coke when burned, reducing the production of flammable volatile substances. The heat loss of flame retardant materials during combustion was significantly reduced, but the smoke density of flame retardant materials during combustion increased compared to those without flame retardant. Based on the above facts, some flame retardant mechanisms have been proposed. The flame retardant effect of phosphorus compounds in different reaction zones can be divided into condensed phase flame retardant mechanism and vapor phase flame retardant mechanism. Organic phosphorus flame retardants play a flame retardant role in condensed phase, and their flame retardant mechanism is as follows: during combustion, phosphorus compounds decompose to form a non flammable liquid film of phosphoric acid, with a boiling point of up to 300 ℃. At the same time, phosphoric acid is further dehydrated to form metaphoric acid, which then polymerizes to form polyphosphoric acid. In this process, not only does the covering layer generated by phosphoric acid have a covering effect, but also because the generated polyphosphoric acid is a strong acid and a strong dehydrating agent, it dehydrates and carbonizes the polymer, changing the mode of polymer combustion and forming a carbon film on its surface to isolate air, thereby exerting a stronger flame retardant effect. The flame retardant effect of phosphorus based flame retardants is mainly reflected in the polymer decomposition stage in the early stage of a fire, as it can promote the dehydration and gasification of polymers, thereby reducing the amount of flammable gases produced by the thermal decomposition of polymers, and the generated carbon film can also isolate external air and heat. Generally, phosphorus based flame retardants have the best effect on oxygen-containing polymers and are mainly used in hydroxyl containing polymers such as cellulose, polyurethane, polyester, etc. For hydrocarbon polymers without oxygen, the effectiveness of phosphorus based flame retardants is relatively small. Phosphorus containing flame retardants are also a type of free radical scavenger. Using mass spectrometry technology, it has been found that any phosphorus containing compound forms PO · during polymer combustion. It can bind with hydrogen atoms in the flame area to suppress the flame. In addition, the moisture generated by phosphorus based flame retardants during the flame retardant process can lower the temperature of the condensed phase and dilute the concentration of combustibles in the gas phase, thereby better achieving flame retardancy.
3.3 Flame retardant mechanism of inorganic flame retardants Inorganic flame retardants include flame retardants based on aluminum hydroxide, magnesium hydroxide, expanded graphite, borate, aluminum oxalate, and zinc sulfide. Aluminum hydroxide and magnesium hydroxide are the main types of inorganic flame retardants, which have the characteristics of non toxicity and low smoke. They absorb a large amount of heat from the combustion zone due to thermal decomposition, causing the temperature of the combustion zone to drop below the critical temperature for combustion and self extinguishing. The metal oxides generated after decomposition mostly have high melting points, good thermal stability, and cover the surface of the combustion solid phase to block heat conduction and radiation, thus playing a flame retardant role. Simultaneously decomposing produces a large amount of water vapor, which can dilute combustible gases and also serve as a flame retardant. Hydrated alumina has good thermal stability and can be converted into AlO (OH) after heating at 300 ℃ for 2 hours. It does not produce harmful gases when in contact with flames and can neutralize acidic gases released during polymer pyrolysis. It has the advantages of low smoke production and low cost, making it an important variety of inorganic flame retardants. Hydrated alumina releases chemically bound water upon heating, absorbs combustion heat, and lowers combustion temperature. When exerting flame retardant effects, it is mainly the action of two crystal waters. In addition, the dehydration product is activated alumina, which can promote the carbonization of some polymers during combustion, thus having a condensed phase flame retardant effect. From this mechanism, it can be inferred that when using hydrated alumina as a flame retardant, the amount added should be relatively large. The main variety of magnesium flame retardant is magnesium hydroxide, which is a type of flame retardant being developed both domestically and internationally in recent years. It undergoes endothermic decomposition reaction at around 340 ℃ to generate magnesium oxide, with maximum weight loss at 423 ℃ and termination of decomposition reaction at 490 ℃. According to the calorimetry method, the reaction absorbs a large amount of heat energy (44.8 kJ/mol), and the generated water also absorbs a large amount of heat energy, reducing the temperature and achieving flame retardancy. Magnesium hydroxide has better thermal stability and smoke suppression ability than hydrated alumina, but due to its high surface polarity and poor compatibility with organic compounds, it needs to undergo surface treatment before it can be used as an effective flame retardant. In addition, its high thermal decomposition temperature makes it suitable for flame retardancy of polymers with high decomposition temperatures such as thermosetting materials. At high temperatures, the embedded layer in expandable graphite is easily decomposed by heat, producing gases that rapidly expand the interlayer spacing of graphite to several tens to hundreds of times its original size. When expandable graphite is mixed with polymers, a tough carbon layer can be formed on the surface of the polymer under the action of flames, thereby playing a flame retardant role. Borate flame retardants include borax, boric acid, and zinc borate. At present, zinc borate is mainly used. Zinc borate begins to release crystalline water at 300 ℃, and under the action of halogen compounds, it generates boron halides and zinc halides, which inhibit and capture free hydroxyl groups and prevent combustion chain reactions; Simultaneously forming a solid covering layer, isolating the surrounding oxygen, preventing the flame from continuing to burn, and having a smoke suppression effect. Zinc borate can be used alone or in combination with other flame retardants. At present, the main products include fine-grained zinc borate, heat-resistant zinc borate, anhydrous zinc borate, and high water zinc borate. Aluminum oxalate is a crystalline substance derived from aluminum hydroxide, with low alkali content. When high polymers containing aluminum oxalate burn, they release H2O, CO, and CO2 without generating corrosive gases. Aluminum oxalate can also reduce smoke density and smoke generation rate. Due to the low alkali content of aluminum oxalate, the use of its flame-retardant coating material for wires and cables does not affect the electrical properties of the material. There are currently 5 developed flame retardants based on zinc sulfide, of which 4 are used for hard PVC and the other can be used for soft PVC, polyolefin and nylon. Such flame retardants can improve the anti-aging performance of materials, have good compatibility with glass fiber and improve the thermal stability of polyolefin.
3.4 Synergistic flame retardant mechanism of mixed use of flame retardants. The combination of halogen containing flame retardants and phosphorus containing flame retardants can produce significant synergistic effects. For the synergistic effect of halogen phosphorus flame retardancy, it has been proposed that the combination of halogen phosphorus can promote decomposition and form halogen phosphorus compounds and their derivatives PBr3, PBr ·, POBr3, etc., which have stronger flame retardant effects than using them alone. The study on the synergistic effect of halogen and phosphorus using methods such as pyrolysis gas chromatography, differential thermal analysis, differential scanning calorimetry, oxygen index determination, and flame retardant programmed temperature observation showed that the decomposition temperature of the flame retardant when used in combination with halogen and phosphorus was slightly lower than when used alone, and the decomposition was very intense. The smoke cloud formed by the chlorine phosphorus compounds and their hydrolysis products in the combustion zone could stay in the combustion zone for a long time, forming a strong gas phase isolation layer. The research on the mechanism of phosphorus nitrogen interaction is not comprehensive enough. It is generally believed that the use of nitrides (such as urea, cyanamide, guanidine, dicyandiamide, hydroxymethyl melamine, etc.) can promote the phosphorylation reaction between phosphoric acid and cellulose. The formed phosphoamines are more prone to esterification of cellulose, and the thermal stability of these esters is better than that of phosphate esters. The phosphorus nitrogen flame retardant system can promote the decomposition of sugars into coke and water at lower temperatures, and increase the production of coke residue, thereby improving the flame retardant effect. Phosphides and nitrides form an expansive coke layer at high temperatures, which serves as a thermal insulation and oxygen blocking protective layer, while nitrogen-containing compounds act as foaming agents and coke reinforcing agents. Basic elemental analysis reveals that the residue contains three elements: nitrogen, phosphorus, and oxygen, which form a thermally stable amorphous material at flame temperature, resembling a glass body, serving as an insulating protective layer for cellulose. Antimony trioxide cannot be used alone as a flame retardant (except for halogenated polymers), but when used in combination with halogenated flame retardants, it has a significant synergistic enhancement effect. This is because antimony trioxide, when burned in the presence of halides, produces antimony halides such as SbCl3 and SbBr3 with a high relative density. These halides cover the surface of the polymer and also have the ability to capture free radicals in the gaseous state. For example, when antimony trioxide is used in combination with chlorine based flame retardants, the chloride decomposes into hydrogen chloride upon heating. Hydrogen chloride reacts with antimony trioxide to form antimony trichloride and antimony oxychloride, and antimony oxychloride continues to decompose upon heating to form antimony trichloride. The combination of hydrated zinc borate and halogenated flame retardants has a good synergistic effect. Under combustion conditions, almost all flame retardant elements can exert flame retardant effects through interactions between them and their decomposition products. Hydrated zinc borate reacts with halogenated flame retardants to produce zinc dihalide and boron trihalide, which can capture HO · and H · in the gas phase and form a glassy isolation layer in the solid phase, providing insulation and oxygen isolation. The generated water dilutes the oxygen in the combustion zone and carries away the heat of reaction, thus exerting a significant flame retardant effect.
3.5The flame retardant mechanism of the 3.5 expansion system. The main components of the expansion type flame retardant system can be divided into three parts: acid source, carbon source, and gas source. Acid sources are generally inorganic acids or compounds that generate inorganic acids when heated to 100 ^ -250 ℃, such as phosphoric acid, sulfuric acid, boric acid, various ammonium phosphate salts, phosphate esters, and borates; Carbon source (charring agent) is the basis for forming foam carbonization layer, which is generally carbon rich polyhydroxy compounds, such as starch, pentaerythritol, its dimer, trimer and organic resin containing light radicals; The gas source (foaming source) is mostly amine or amide compounds, such as melamine, melamine, polyphosphate amine, etc. The structure of carbon formation in the expansion system is complex and influenced by numerous factors. The chemical structure and physical properties of the polymer body, the composition of the expansion flame retardant, the conditions during combustion and cracking (such as temperature and oxygen content), the reaction rate of crosslinking, and many other factors can all affect the structure of the expanded carbon. The thermal protection effect of the expanded carbon layer depends not only on the coke yield, carbon layer height, carbon layer structure, and thermal stability of the protective carbon layer, but also on the chemical structure of the carbon layer, especially the appearance of cyclic structures that increase thermal stability, as well as the strength of chemical bonds and the number of cross-linking bonds. It is generally believed that the flame retardant mechanism of the expansion system is condensed phase flame retardant. Firstly, polyphosphate amine is thermally decomposed to generate phosphoric acid and pyrophosphate with strong dehydration effect, which esterizes pentaerythritol and then dehydrates and carbonizes it. The water vapor formed by the reaction and the ammonia gas decomposed by melamine cause the carbon layer to expand, ultimately forming a layer of microporous carbon layer, which isolates air and heat conduction, protects the polymer body, and achieves the purpose of flame retardant. The addition of expandable flame retardants to polymer materials must possess the following properties: good thermal stability, able to withstand high temperatures above 200 ℃ during polymer processing; Due to the release of a large amount of volatile substances and the formation of residues during thermal degradation, this process should not have adverse effects on the expansion and foaming process; This type of flame retardant is uniformly distributed in polymers and can form a layer of expanded carbon that completely covers the surface of the material during combustion; Flame retardants must have good compatibility with the flame retardant polymer, and must not have adverse effects on the polymer and additives, nor excessively deteriorate the physical and mechanical properties of the material. The advantages of expandable flame retardants over general flame retardants are halogen-free and antimony oxide free: low smoke, less toxic, and non corrosive gases; The carbon layer generated by the expansion flame retardant can adsorb the melted and ignited polymer, preventing it from dripping and spreading the fire
3.6The flame retardant mechanism of ammonium salts is poor. Ammonium salts have poor thermal stability and release ammonia gas when heated, such as [NH4) 2SO4. The decomposition process is as follows: [NH4) 2SO4 → NH4HSO4 NH4HSO4 → H2SO4+NH3 ↑. The released ammonia gas is a non flammable gas that dilutes oxygen in the air; The formed H2SO4 acts as a catalyst for dehydration and carbonization. It is generally believed that the latter effect is the main one In addition, experiments have shown that NH3 undergoes the following reactions in fire: NH3+O2 → N2+H2O, accompanied by deep oxidation products such as N2O4. It can be seen that NH3 not only has a physical flame retardant effect, but also a chemical flame retardant effect.
3.7The flame retardant mechanism of nanocomposite materials is proposed separately. Although both belong to composite flame retardant, their principles are slightly different. Nanocomposite materials refer to the dispersion of one or more components of a material at the nanoscale or molecular level in another component matrix, and this research has only a history of over a decade. Experiments have shown that due to the ultrafine size of nanomaterials, the performance of various types of nanocomposites is significantly improved compared to their corresponding macroscopic or micrometer level composites, and the thermal stability and flame retardant properties of the materials are also greatly improved. Some scale like inorganic substances can be fragmented into nanoscale structural micro regions under physical and chemical action, with interlayer spacing generally ranging from a few tenths to a few nanometers. They not only allow certain polymers to intercalate into the nanoscale interlayer space, forming "intercalation type nanocomposites", but also the inorganic interlayer is stretched by the polymer to form a large aspect ratio single piece inorganic substance, uniformly dispersed in the polymer matrix, forming "layer release type nanocomposites". By utilizing the characteristics of porous or layered inorganic compounds, inorganic/polymer nanocomposites can be prepared. During thermal decomposition and combustion, a multi-layer structure of carbon and inorganic salts may be formed, which serves as insulation and prevents the escape of combustible gases, enabling the high polymer to be flame retardant. In addition, the use of inorganic/polymer nanocomposites also has the functions of corrosion resistance, leakage prevention, wear resistance, and weather resistance. At present, gratifying achievements have been made in the research of nanocomposites such as nylon/clay nanocomposites, PS/clay nanocomposites, PET/clay nanocomposites, PBT/clay nanocomposites, PP/clay nanocomposites, etc.
3.8The research on using silicone compounds as flame retardants began in the early 1980s. In 1981, Kamber et al. published a research report on the improvement of flame retardancy by blending polycarbonate with polydimethylsiloxane. Although the research and development of organic silicon flame retardants lags behind halogen and phosphorus flame retardants, organic silicon flame retardants, as a new type of halogen-free flame retardant, have unique characteristics due to their excellent flame retardancy, processability, and environmental friendliness. Silicone flame retardants include silicone oil, silicone resin, polysiloxane with functional groups, polycarbonate siloxane copolymer acrylate siloxane composite materials and silicon gel. Polymer materials that are flame retardant with silicone compounds tend to migrate to the surface of the material, forming a polymer gradient material with a surface enriched with silicone. Once burned, a silicone specific inorganic insulation layer containing one Si-O bond and one Si-C bond is generated, which not only prevents the decomposition products generated by combustion from escaping, but also inhibits the thermal decomposition of polymer materials, achieving the goal of high flame retardancy, low smoke emission, and low harmfulness. At present, the organic silicon flame retardants being developed and applied include the "D.C. RM" series flame retardants developed and commercialized by Dow Corning in the United States, the silicone flame retardant "XC-99-B6645" jointly developed by NEC and GE Toshiba Organic Silicon in Japan, and SFR104 organic silicon resin developed by GE in the United States.
Supplementary Information
1The composition of an expanding flame retardant is mainly composed of three parts: carbonization agent (carbon source), carbonization catalyst (acid source), and expansion agent (gas source). Carbonization agents are the carbon source for expanding porous carbon layers, generally consisting of carbon rich multifunctional groups (such as - OH). Pentaerythritol (PER) and its di - and tri alcohols are commonly used carbonization agents. Carbonization catalysts are generally compounds that can release inorganic acids under heating conditions. Inorganic acids require a high boiling point and not too strong oxidizing properties. Ammonium polyphosphate (APP) is a commonly used carbonization catalyst. Expansion agents are compounds that release inert gases when heated, typically ammonium and amide substances such as urea, melamine, melamine, and their derivatives. The selection criteria for each component are as follows:
1)Acid source: In order to be practical, the acid source must be able to dehydrate the carbon containing polyol. Before a fire occurs, we do not want dehydration reactions to occur, so the commonly used acid sources are salts or esters. The release of acid from the acid source must be carried out at a lower temperature, especially below the decomposition temperature of the polyol. If the organic part helps to form charcoal, using organic phosphides has a better effect.
2)Carbon source: The effectiveness of carbon source is related to the carbon content and the number of active hydroxyl groups. The carbon source should react with the catalyst at a lower temperature before its own or matrix decomposition.
3)Gas source: The foaming agent must decompose at an appropriate temperature and release a large amount of gas. Foaming should occur after melting and before solidification. The appropriate temperature is related to the system. For specific flame-retardant polymer systems, sometimes it is not necessary for all three components to exist simultaneously, and sometimes the polymer itself can act as one of the elements. The above criteria can be used to predict the effectiveness of most systems.
2)Flame retardant mechanism: When the expansion type flame retardant is heated, the carbonization agent dehydrates into carbon under the action of the carbonization catalyst, and the carbide forms a fluffy and porous closed carbon layer under the action of the gas decomposed by the expansion agent. Once formed, it is non flammable and can weaken the heat conduction between the polymer and the heat source, and prevent gas diffusion. Once sufficient fuel and oxygen are not obtained during combustion, the burning polymer will self extinguish. This carbon layer undergoes the following steps to form.
(1) At lower temperatures, inorganic acids that can esterify polyols and act as dehydrating agents are released from the acid source.
(2) At temperatures slightly above the release of acid, esterification occurs, and amines in the system can serve as catalysts for esterification.
(3) The system melts before or during esterification.
(4) The water vapor generated by the reaction and the non combustible gas produced by the gas source cause the molten system to expand and foam.
(5) When the reaction is nearly completed, the system gelatinizes and solidifies, and finally forms a porous foam carbon layer. Based on the above discussion, it seems that any compound containing these functional groups can foam, but the degree of foaming varies, which is actually incorrect. In order to foam, each reaction step must occur almost simultaneously, but must be carried out in a strict order. Expanded flame retardants may also have gas-phase flame retardant effects, as the phosphorus nitrogen carbon system may produce NO and NH3 when heated, which can also cause free radicals to bind and terminate the combustion chain reaction.
The three factors that affect the effectiveness of expansion flame retardants depend on the carbonization reaction, expansion reaction, and carbon layer structure.
3.1 Charcoal Formation Reaction The carbonization effect of expansive flame retardants is mainly due to the thermal decomposition of acid source APP, which generates phosphoric acid and pyrophosphate with strong dehydration properties. They undergo dehydration or deamination reactions with hydroxyl or amino groups in the carbonization agent to form phosphate esters. The generated esters undergo thermal decomposition to produce unsaturated olefins, which then undergo multi molecular cyclization polymerization to form stable polyaromatic carbon layers, while the alkyl branches in non aromatic structures break down into small molecules and burn. The carbonization reaction process of common APP and PER systems is carried out in several steps. Firstly, at 210 ℃, the APP long-chain breaks and forms phosphate bonds. After losing water and ammonia, cyclic phosphate esters can be generated. If the temperature continues to rise, through carbonization reaction, the phosphate ester bond is almost completely broken, forming an unsaturated rich carbon structure. Diels Aider reaction may occur during the reaction, causing cyclic olefins, aromatic hydrocarbons, and condensed hydrocarbon structures to enter the coke structure.
3.2 Expansion Reaction Expansion is caused by the migration of gases generated by cracking. The migration rate is related to the viscosity of the molten material in the combustion zone and the amount of gas released. The viscosity of the polymer can be adjusted by controlling the crosslinking degree to affect the carbon structure. The shape of the enclosed chamber of the expanded carbon layer will depend on the amount of gas released during carbonization and the viscosity of the carbonized material. The expansion agent must match the gas release process with the carbonization process. The decomposition temperature of the foaming source is too low, and the gas has already overflowed before carbonization, which cannot play a foaming role; The decomposition temperature of foaming is too high, and the gas may lift or blow away the carbon layer. Urea cannot be well matched with the APP-PER system. Although urea can release 70% of its gas, its decomposition temperature (150-230 ℃) is too low compared to the formation temperature of the expansion layer (APP-PER) (280-320 ℃). Melamine can undergo a series of reactions at 250-380 ℃, releasing gas, and is a commonly used expansion agent. In addition, the PER phosphate ester structure and PER ether structure generated by carbonization reaction also exhibit expansion phenomenon when heated.
3.3The carbon in the carbon layer expansion system is generated by incomplete cracking or oxidation of polymers at lower temperatures. The formation rate of charcoal is fast and involves thermal oxidation. The complex structure formed by this charcoal can serve as a barrier for the passage of decomposed gases and molten polymers. The expansion ratio, expansion rate, strength, and composition of the carbon layer are also important factors affecting the quality of the carbon layer. According to reports, some physical properties of the carbon layer, such as mechanical strength, continuity, pore opening and closing, gas and liquid penetration, are more effective than expansion. SEM shows that after adding inorganic additives, the honeycomb like carbon structure tends to crack, leading to a decrease in oxygen index. Therefore, to ensure good flame retardancy, the size of the small chamber should be controlled within a certain range. This is because although air in the chamber can reduce thermal conductivity, if the chamber volume is too large, air convection can increase thermal conductivity. The increase in thermal conductivity leads to accelerated thermal degradation, thereby reducing the flame retardant effect.