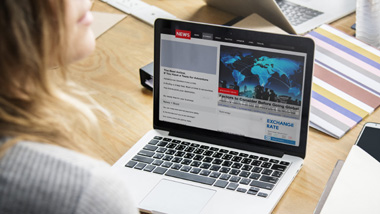
NEWS
一、inorganic flame-retardant
The flame retardant mechanism of inorganic flame retardants is to lower the system temperature by releasing water vapor through thermal decomposition. At the same time, water vapor dilutes flammable gases to achieve flame retardant effect. Its flame retardant effect is determined by the amount of water vapor, so the flame retardant effect is related to the amount of flame retardant.(一)metal hydroxide
Inorganic flame retardants are halogen-free flame retardants with advantages such as high safety, smoke suppression, non toxicity, and low cost. They are mainly composed of aluminum hydroxide and magnesium hydroxide. Currently, inorganic flame retardants are widely used abroad, with the United States, Japan, and Western Europe accounting for 60%, 64%, and 50% of the total flame retardant consumption, respectively.
Because magnesium hydroxide has many excellent characteristics, basic and applied research on magnesium hydroxide has been very active at home and abroad in the past 10 years. Currently, there are more than 20 enterprises from nearly 10 countries producing more than 20 varieties, with a total annual production capacity of about 170000 tons.Many countries are still building or planning to build new magnesium hydroxide facilities. The main domestic manufacturers include Shandong Jiaozhou Guhe Magnesium Salt Factory, Shanghai Zhentai Chemical Factory, Hebei Wuyi County Flame Retardant Factory, Jiangsu Nanhua Group Lianyungang Alkali Factory, Shandong Haihua Group, etc.
Average dispersion has become the most important issue in processing engineering. Selecting high-performance surface modifiers for the surface modification of magnesium hydroxide is the primary task before its use. The purpose is to improve the surface activity of particles, enhance dispersion, improve flame retardancy, enhance compatibility with polymer materials, improve impact resistance and thermal energy.
When aluminum hydroxide and magnesium hydroxide are used alone as flame retardants, the dosage is generally between 40% and 60%, which seriously affects the mechanical properties of the materials.
Aluminum hydroxide and magnesium hydroxide are both white powders with a relative density of around 2.4 and a particle size of 1-20 μ m. Aluminum hydroxide begins to dehydrate at a temperature of 200 ℃, while magnesium hydroxide begins to dehydrate at a temperature of 340 ℃. Magnesium hydroxide has a high thermal decomposition temperature, 140 ℃ higher than aluminum hydroxide, which allows synthetic materials with added magnesium hydroxide to withstand higher processing temperatures, accelerate extrusion speed, shorten molding time, and improve flame retardant efficiency. Magnesium hydroxide has a fine particle size, which reduces equipment wear and is beneficial for extending the service life of processing equipment. Because magnesium hydroxide has many advantages compared to aluminum hydroxide, the proportion of magnesium hydroxide is increasing. Compared with similar inorganic flame retardants, magnesium hydroxide has better smoke suppression effect. Magnesium hydroxide has no harmful substance emissions during production, use, and disposal processes, and can also neutralize acidic and corrosive gases generated during combustion.
(二)Inorganic phosphorus series
1、Red phosphorus masterbatch
Red phosphorus masterbatch is used for flame retardancy of materials lacking oxygen elements such as general plastics, rubber, polyethylene, polypropylene, etc. It is best to use it in combination with magnesium hydroxide and aluminum hydroxide; Used for flame retardancy of oxygen rich materials such as PET, PC, PBT, PA, etc., and can be used independently; During the processing, in order to achieve the best dispersibility of red phosphorus, a certain amount of dispersant can be compounded.
The main disadvantage of red phosphorus masterbatch is its color tone, which cannot provide products with more color options besides dark red and black.
Red phosphorus masterbatch is a dark red particle made by compounding red phosphorus with inorganic flame retardants such as aluminum hydroxide and expanded graphite, and using a matrix resin as a carrier. The safety issue has been solved. It has low smoke and high flame retardant efficiency; No dust pollution, excellent processing function; Low density, good thermal stability, and minimal physical function degradation of the product; No frosting, migration, or erosion of the mold during the processing. Especially products with high resistance to leakage trace index (CTI) have significant advantages in electronic and electrical applications.
Red phosphorus is a good flame retardant among non halogenated flame retardants, with advantages such as low addition amount and wide application. Ordinary red phosphorus is prone to moisture absorption, has poor compatibility with polymer materials, and is particularly prone to spontaneous combustion, making it unsuitable for practical use. Microencapsulated red phosphorus flame retardant reduces the activity of red phosphorus and solves compatibility. The red phosphorus content is around 85%, but the problem of spontaneous combustion has not been effectively solved, and dust pollution is severe.
The currently commercialized varieties include: ClariantWC's ExolitRP, Albright&Wilson's AMGARD and AMGARDCPC series, AmgardCRP and AmgardGHT series, Japan's RINKA series, etc.
In addition, red phosphorus has a smoke suppression effect, and suitable smoke suppressants can be found to be compounded with it. Smoke suppression is more important than fire prevention in fires, promoting the development of smoke suppression technology.
2.ammonium phosphate
3.Ammonium polyphosphate
Ammonium polyphosphate (APP) is a high-performance inorganic phosphorus flame retardant and is currently an active research field in phosphorus based flame retardants. The P-N flame retardant element content of the APP is high, the thermal stability is good, and the product is almost neutral; In addition, it is inexpensive, has low toxicity, and has long-lasting flame retardant properties. It can be used alone or in combination with other flame retardants for the flame retardancy of plastics. In addition, polyphosphate is a strong dehydrating agent that can dehydrate and carbonize polymers to form a carbon layer, isolating the contact between polymers and oxygen, and preventing combustion in the solid phase [8].
APP is a good flame retardant for polyolefin, protective coating of steel structure, adhesive cement, sealant, PU foam, phenolic, unsaturated polyester and epoxy resin used for composite materials, fabrics, paper and wood. Organic phosphate ester is required for higher thermal stability.
Although ammonium polyphosphate is low-cost, easy to use, and has good flame retardant effects, with the continuous development of its application fields, it has also exposed some of its disadvantages, such as easy moisture absorption in the air, sticky hand feel, and significant impact on the strength of cotton fabrics. When used for paper, it will make the paper yellow and brittle. The microencapsulation of ammonium polyphosphate can alleviate a series of adverse effects mentioned above. Another way to improve the overall flame retardant effect of ammonium polyphosphate is to use coupling agents, such as surface treatment with silicon containing compounds, to make it a fine powder with flowability, enhance its compatibility with plastics and processing flowability, and improve its flame retardancy. On the other hand, increasing the polymerization degree of ammonium polyphosphate can also enhance its overall flame retardant effect. According to reports [9], APP with a P content of 30.5% has higher flame retardancy when combined with pentaerythritol. At the same time, AP has good synergistic effects with metal oxides (such as manganese dioxide), inorganic fillers (zeolites), and other flame retardants. Ammonium polyphosphate is a white powder with a decomposition temperature above 256 ℃. Ammonium polyphosphate is cheaper than organic flame retardants, less toxic, and has good thermal stability. It can be used alone or in combination with other flame retardants. The expansion flame retardant system based on long-chain ammonium polyphosphate is currently a hot topic in the research of halogen-free flame retardant polyolefins, and has shown good development prospects in polyolefin processing modification.
二、organic flame retardant
(一)Organic phosphorus series
1.phosphate:
Phosphate ester series mostly belong to additive flame retardants. Due to its abundant resources, low price, and good compatibility with high polymers, phosphate esters are widely used in organic phosphorus flame retardants. The characteristics of phosphate esters are their dual functions of flame retardancy and plasticization. It can achieve halogen-free flame retardants. The plasticizing function can improve the flowability and processability of plastics during molding, and can suppress residual materials after combustion. The main products include toluene diphenyl phosphate CDP, triisopropylphenyl phosphate IPPP, TCP, TPP, etc.
TCP has significant neurotoxicity to humans and high viscosity. TPP precipitates when heated and is volatile, causing metal contamination in plastics with high forming temperatures such as engineering plastics, which may worsen the working environment. Therefore, nowadays toluene diphenyl phosphate (CDP) is gradually replacing it.
The CDP addition amount is generally between 15% and 22%, and the UL94 level reaches V-O level
2.Phosphonate esters: resorcinol bis (diphenyl phosphate) RDP, BDP,
At present, many flame retardant manufacturers and research institutions in China have conducted extensive research on the industrial production of resorcinol bis (diphenyl phosphate) RDP, and have carried out small-scale trial production. Major domestic manufacturers include Zhejiang Wansheng and Yak Chemical. The main overseas sales manufacturer is Great Lakes products from the United States.
When used, resorcinol bis (diphenyl phosphate) is generally used alone and does not need to be combined with other flame retardants. It is mainly used for some high-performance styrene copolymers, such as PPO/HIPS and PC/ABS. When flame retardant PPO/HIPS is used, the dosage is around 11%, the oxygen index reaches 37%, and the UL94 grade (1.6mm) reaches V-O and grade. When flame retardant PC/ABS alloy is used, it is related to the ratio of PC/ABS, and the dosage is generally between 6% and 10%. The oxygen index reaches 29%, and the UL94 level (1.6mm) reaches V-O.
It has the characteristics of high flame retardancy, low dosage, and minimal impact on the physical properties of the finished product. It has dual functions of flame retardancy and plasticization, which can make flame retardants completely halogen-free, improve the activity processing function in plastic molding, reduce erosion, improve thermal aging function, improve thermal deformation temperature, and suppress residual materials after combustion.
Resorcinol bis (diphenyl phosphate) is a high molecular weight organic phosphine flame retardant that appears as a clear liquid; It has a high phosphorus content, with a phosphorus content of 10.8%.
The main BDP manufacturers are Shandong Murray Chemical and Zhejiang Wansheng
(二)nitrogenated flame retardant
DSMMelapur, a Dutch company, is the most well-known producer of nitrogen based flame retardants internationally. Its product is Melapur? MC、Melapur? MP、Melapur? 200 series. Nowadays, there are many additive factories in China that produce nitrogen based flame retardants MC series, but the product quality is average.
Nitrogen based flame retardants are currently mainly used in polyolefins and polyamides, and do not need to be used in combination with other flame retardants. For non reinforced nylon, the flammability level can reach UL94V-O level when the addition amount is 8%; For PP, the flammability level can reach UL94V-O level when the addition amount is 25%; Excellent cost/function ratio. Dutch DSM product Melapur? 200 is a nitrogen based flame retardant suitable for glass fiber reinforced PA66, and its flammability level can reach UL94V-O level when added at a dosage of 25%. And the processing temperature can reach up to 320 ℃.
Nitrogen based flame retardants are melamine and its compounds with phosphorus, mainly melamine, melamine cyanuric acid, and melamine phosphate, which are the most promising varieties in the flame retardant market. Nitrogen based flame retardants are generally white crystalline fine powders with particle sizes ranging from 10 μ m to 50 μ m, which are easily dispersed. Density ranging from 1.5cm to 1.7g/cm. As a new type of flame retardant, nitrogen based flame retardants have many advantages: efficient flame retardancy; Does not contain halogens; No erosive effect, thus reducing the problem of mechanical erosion; UV resistance; The motor has good performance, and it has the most significant advantage in electronic and electrical products; Not fading, not spraying frost; Recyclable and reusable.
三、Halogenated flame retardant
(一)At present, nearly 80% of the flame retardants used for plastic modification in China are halogenated flame retardants, represented by polybrominated diphenyl ethers and polybrominated biphenyls. Bromine based flame retardants have high efficiency, low dosage, minimal impact on material functionality, and moderate price. Compared with other types of flame retardants, its efficiency/price ratio is more superior. 70% to 80% of China's electronic and electrical products for export use this type of flame retardant. However, the bromine antimony flame retardant system will naturally produce a large amount of smoke and corrosive gases during thermal cracking and combustion. In recent years, some EU countries have believed that the combustion of bromine flame retardants will produce toxic and carcinogenic polybrominated dibenzofuran (PBDD) and polybrominated dibenzofuran (PBDF). In February 2003, the EU issued two bans, RoHS and WEEE, among which RoHs is the Restriction of Hazardous Substances Directive, which stipulates that from January 1, 2006, all electronic and electrical equipment sold in EU countries cannot contain polybrominated biphenyls and polybrominated diphenyl ethers.
(二)Environmentally friendly brominated flame retardants
Brominated epoxy resin
The Dead Sea Bromine Company in Israel is the most well-known international producer of brominated epoxy resin flame retardants, with a complete production process and excellent product quality; Once the only brand in the domestic and international brominated epoxy resin flame retardant market. Since 2002, Shandong Laiyu Chemical and others have successively commercialized brominated epoxy resin, but the product quality is not satisfactory. At present, representative products in the domestic market include: Israel Dead Sea Bromine Company F2100F2400, Shandong Laiyu Chemical, Taiwan Changchun BEB series, etc.
It needs to be used in conjunction with antimony compounds during use.
Low phase molecular weight brominated epoxy resin is used for flame retardant ABS and HIPS, while high phase molecular weight is suitable for flame retardant ABS/PC alloys and engineering plastics such as PC, PET, PBT, etc.
Brominated epoxy resin, also known as tetrabromobisphenol A epoxy resin oligomer, is used as a flame retardant with a bromine content of up to 50% and a molecular weight between 1000 and 45000. It is divided into EP and EC types; Compared with EC type, EP type has better light resistance but lower bromine content, while the latter flame retardant ABS and HIPS have better impact strength. The trade product brominated epoxy resin is a mixture of milky yellow semi transparent chips and white powder. Domestic brominated epoxy resin has a pungent odor, while Israeli Dead Sea bromine products have no odor. Brominated epoxy resin has satisfactory melt flow rate and high flame retardant efficiency, excellent thermal and optical stability, and can endow flame retardant substrates with good mechanical properties, and the product does not frost.
The first company to industrialize the 8010 was Albemarle Corporation in the United States, which applied for production and use patents; This once delayed the research and production units of flame retardants in China, but after investigation, it was found that Yabao Company's patent scope is outside of China, so it can produce and use 8010 in China, but cannot export or apply for patents. Amidst the darkness, a bright future emerged, and domestic research and production units invested in research. By the end of 2002, the industrial scale experiment was successfully conducted. At present, representatives of domestic market manufacturers include Yabao Company, Dahu Company, Gusu Jinghua Industrial Co., Ltd., Shandong Laiyu Chemical, etc.
As an additive bromine based flame retardant, 8010 also needs to be used in combination with antimony compounds, with the same proportion as DBDPO/antimony compounds; Compared with DBDPO, 8010 is more suitable for engineering plastics with high temperature and high viscosity properties.
2、Decabromodiphenyl ethane 80108010 does not belong to polybrominated diphenyl ethers, and it is absolutely impossible to produce PBDD or PBDF during combustion; The relative molecular weight of 8010 is 971; The bromine content is 82%, which is equivalent to the bromine content of DBDPO (83%), so the flame retardant function is basically the same; The initial melting point is 345 ℃, and its thermal stability is higher than DBDPO (305 ℃); Its light resistance and resistance to dialysis are superior to DBDPO, and the most valuable feature is that its flame-retardant plastic can be recycled, which is a characteristic that many bromine based flame retardants do not possess. 8010 industrial products are white crystalline powders with uniform particle size of 3 μ m, free movement, and micro granulation. They are easily dispersed in plastic modification, and the color of plastic products is free. Moreover, the industrialization cost is commensurate with DBDPO, making it the most ideal replacement for DBDPO.
3.Brominated polystyrene
Great Lakes Company and Albemarle Company are well-known producers of brominated polystyrene, and their products were once far ahead in the domestic market. Now some flame retardant manufacturers in China have started domestic production, such as Shouguang Marine Chemical Co., Ltd.
Brominated polystyrene is mainly used in thermoplastic resins such as PA, PBT, PET, etc., and needs to be used in conjunction with antimony compounds during the usage process. When adding flame-retardant polyester, a dosage of 13% (reinforced) to 17% (non reinforced) can give the material UL94V-O grade (0.8mm). When adding flame-retardant polyamide, a dosage of 21% can give the material UL94V-O grade (0.8mm).
Brominated polystyrene is named brominated polystyrene and polybrominated styrene according to its synthesis pathway. From the naming, it can be seen that brominated polystyrene is achieved by brominating polystyrene; Polybrominated styrene is synthesized by first raising the precursor vinyl bond of styrene, then brominating it, restoring the vinyl bond, synthesizing brominated styrene, and then polymerizing it again. From whether solvents are used in the synthesis process, it can be divided into solvent method and non solvent method. Because the solvent method consumes less bromine, people usually use the solvent method for synthesis.
The development of brominated polystyrene is similar to that of brominated epoxy resin, and it is also a rapidly developing flame retardant variety in recent years. Brominated polystyrene is a white or pale yellow powder or particle with a bromine content of around 60%. The thermal decomposition temperature is greater than 310 ℃, and it has the advantages of high molecular weight, good thermal stability, good dispersibility and miscibility in polymers, easy processing, and no frosting.